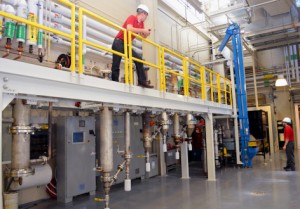
Lysle Whitmer, giving a quick tour of the technical upgrades to an Iowa State University biofuels pilot plant, pointed to a long series of stainless steel pipes and cylinders. They’re called cyclones, condensers and precipitators, he said, and there’s an art to getting them to work together.
The machinery is all about quickly heating biomass (including corn stalks, switchgrass or wood chips) without oxygen to produce solid biochar and liquid bio-oil. The former can fertilize crops; the latter can power the economy.
The process is called fast pyrolysis. It’s a thermochemical way to break down plants for the production of advanced biofuels. Whitmer, the senior research engineer for Iowa State’s Bioeconomy Institute, and other Iowa State engineers have been studying the process at the pilot-plant scale for more than 15 years.
And so they have a good understanding of the science and technology of the process.
Now, machinery upgrades supported by $75,000 from the state-supported Leading the Bioeconomy Initiative at Iowa State will help engineers develop an even better understanding of the art of fast pyrolysis.
“The science of pyrolysis is what you can read in a book,” said Robert C. Brown, an Anson Marston Distinguished Professor in Engineering, director of Iowa State’s Bioeconomy Institute and the Gary and Donna Hoover Chair in Mechanical Engineering. “The art of pyrolysis is actually being able to make it work in continuous, pilot-scale reactors. This entails a lot of know-how in addition to book learning.
“The support from the Leading the Bioeconomy Initiative to upgrade our pilot-scale pyrolyzer gives us an edge over our colleagues whose experience is often limited to bench-top reactors in the lab.”
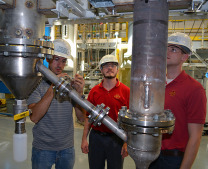
Whitmer said the upgrades are “from the ground up” and have created “Pyrolyzer 2.0” at Iowa State’s BioCentury Research Farm just west of Ames.
A team of graduate and undergraduate engineering students redesigned the machine to improve its efficiency, instrumentation, data collection, reliability and maintenance, Whitmer said. A major focus was making it easier and faster to clean and switch the machine from one experiment to the next. The engineers also wanted to improve the machine’s reliability over long and continuous production runs.
Whitmer said the improvements have bumped the pyrolyzer’s processing rate from 7 kilograms of biomass per hour to 10 kilograms per hour.
One way the engineers expect to increase production is by tweaking how the machine separates and collects fractions of the bio-oil produced by fast pyrolysis. Bio-oil is a complex mix of chemicals and compounds and Whitmer said it’s much easier to process when the heavier fractions are separated from the lighter ones. And now the pilot plant is collecting six fractions instead of five.
“That increases the overall yield of bio-oil and improves the quality of each fraction for recovery of more valuable chemicals like sugars, asphalt-like phenolic oligomers and acetic acid,” Brown said.
Last July, an Iowa State research team led by Brown was awarded a patent for the fractioning process. The technology has been exclusively licensed to Avello Bioenergy Inc., a startup company established by three Iowa State graduates.
Brown said a pilot plant that incorporates what Iowa State engineers have learned about fast pyrolysis could spark even more economic development for Iowa.
“Fast pyrolysis is a pathway to advanced renewable fuels from cellulosic biomass like corn stover, which Iowa has a lot of, and switchgrass, which is well suited to Iowa’s climate and soils,” he said. “What we learn in the lab can help companies commercially develop these Iowa resources.”
January 28, 2014 by Mike Krapfl